Srikrishna Karkare, an IIT Bombay alumnus, spent his formative years at Thermax. He quit in 1988 to start a small trading concern for the chemical and allied industry. His wife Alka, who is also his batchmate from IIT Bombay, continued working with Praj, and was the family financial pillar in the formative years of Enpro. She quit Praj a few years later to join Srikrishna when the work justified their combined presence. The trading concern had decided to integrate backward into manufacturing, based on repeated requests from customers. https://www.enproindustries.in/ has grown today to a 250,000 sq ft factory set in 13 acres of land at Merkel, Pune. Their bread and butter product is lubrication systems for centrifugal compressors and turbines used in the oil and gas sector. They also have a wide range of skid mounted modular heat exchangers, filtration units and chemical injection units. Off late, the company has diversified into pressure vessels and brewery equipment. 70% of the production is exported to over 80 countries.
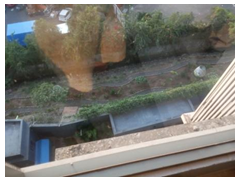
Nallah Park at the back of the building
As Enpro grew over the years, manufacturing also grew. Space in H block fell short, so more space was taken on rent. It soon grew to 3 locations – and coordination was becoming a challenge. Decision was made 15 years ago to consolidate all manufacturing in a single location. 12 acres of land was procured in Merkel – and the shift there happened 10 years ago. The 30,000 sq ft H block premises was converted into a 50,000 sq ft built up area office block which can seat 300 folks. Designed by Landmark architects, it is a LEED platinum rated green building with 100% fresh air circulation and a 150 kW rooftop solar. 80% of energy needs of the Merkel factory are met using solar – and 60% energy needs of office are met by solar. The building uses maximum diffused daylight to reduce lighting load. But it also blocks direct sunlight to manage heat loads.
We visited with Sri to have a dekko. We started with some lovely green tea at his spacious top floor office. Then had a standing meeting with Alka and Anuj, Sri’s son. Anuj, in the Karkare family tradition, finished his graduation from IIT Bombay, and followed it up with a degree in renewable energy from a leading French university and an MBA from Insead. Anuj is a super athlete and has finished an Ironman in NZ.
We mulled over the future of the oil and gas sector, which is Enpro’s largest customer. Unlike popular belief, the sector is still seeing demand growing at 5 to 6 percent a year. Capacity addition though does not follow that graph – as there are years in which demand is allowed to grow – and once it outstrips supply, prices go up. After some period of increased prices, supply side growth takes place and the cycle repeats. Sri feels that peak oil, in terms of demand, is about 10 years away. Apart from new installations, replacement demand will also crop up soon enough. Most of the big oil refineries in the US and Middle East were set up in the seventies – and are due for decommissioning soon. So there should be a boom for capital equipment suppliers soon when the replacement cycle starts.
Most of the oil industry is looking at hydrogen as its saviour. All of them have a similar game plan – invest in solar generation, electrolysers and hydrogen storage and distribution. The sector thinks it will work because it is a centralised energy model that is very similar to the oil DNA. I have my doubts. I think personal mobility space will be the first to be electrified. Internal road transport will shift to railways, the original EVs of the world. Marine will work on hub and spoke models with ships between hubs running on nuclear energy. Aviation will be the last bastion of oil – and probably hydrogen will have some role to play there – though Hindenberg still remains on my mind when it comes to the safety of carrying that kind of fuel onboard a plane.
With the likes of Reliance, a major customer of Enpro, pushing heavily to hydrogen, the team has started working on subsystems in electrolysers which they will supply to OEMs. My advice was to concentrate on building skills in nuclear. They already have an excellent fabrication facility at Merkel. (Must cycle down with Sri, probably last Saturday of November or early December.) And for the power sector, nuclear is the only writing on the wall, after the demise of coal.
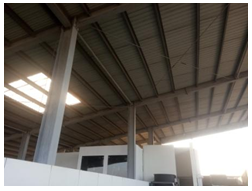
Rooftop Solar
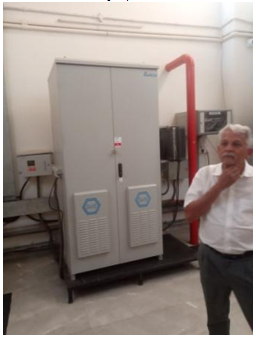
Net Metering Control Panel
We then started a conducted tour of the building. My interest was more on the innovations in energy management in the building. Our first port of call was the roof. As you get onto the roof, the first thing that strikes you is the massive steel structure that houses the south facing 160 kW solar panels. The sloping roof has an angle of almost 20 degree, and the height at the North end is almost 40 ft. Must have taken quite some steel to build the structure. Maybe a design like the self supporting truss less roof at Merkel could have helped. Will require flexible solar panels – and may lead to some loss in energy generation, but should be worth doing some math there about overall capex. Sri shared that the solar panels capex was about Rs. 50 per watt, or Rs. 50,000 per kW. He generates about 5 * 160 = 800 units of electricity a day. That is pumped back into the grid by net metering. There is no storage – and that kind of disappointed me. As there is a 250 kVA genset for backup – which could have been replaced by LFP storage. During power outages, solar has to be augmented by genset, as it requires some base load. And gensets don’t work too well on part loads.
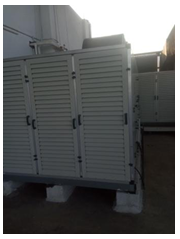
Giant Cooler
The high point of the building is the HVAC system. There are modular units which sit on the roof. Each unit is a kind of giant desert cooler, but instead of the Nagpur style cooler where ducts carried the cooled moisture laden air into the living spaces, these coolers have an additional heat exchanger, where the output of the desert cooler is used to cool another stream of fresh air, without any mixing happening. The advantage is that this cooled air does not have the 100 percent relative humidity which is the problem associated with a desert cooler. There is some water injection done in this air stream to maintain RH at 30%, which is ideal for the human body. This air is then circulated through ducts to the entire building. Most of the energy is used in running the blowers which move air. The main duct alone uses a 60 HP blower. One of the other peculiarities of this design is that energy consumption does not go down too much either with part loads – or with changes in weather. The summer and winter electricity bill for the system is almost the same. Blowers have to be run irrespective of the season, as the entire building is an airtight space. But the big plus is that compared to conventional AC systems, this one consumes 70% less energy. I for one, would still want to see open windows – and some natural circulation of air. Why run blowers on days when you can enjoy natural breeze? There are some ceiling fans installed – these are used mostly in the months of Oct to Dec, when the desert coolers are not able to achieve the cooling thanks to low evaporation rates.
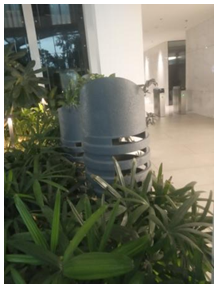
Underground pipe
There is a two stage evaporative cooling with 100% fresh air intake. This further reduces energy consumption by 60% compared to conventional air conditioning. There is a very innovative earth tunnel heat exchanger which uses pipes dug 12 ft into the ground to exchange to pump the building heat into the ground. This operates with a very low power consumption compared to ACs. This earth air heat exchanger was the research topic of a young IIT D alumnus, for his PhD thesis at TERI. Temperature is kept at 26 C with very comfortable 30% relative humidity. (Just to contrast, humidity levels are 100% for desert coolers.) The feeling inside is akin to sitting under a neem tree on a hot afternoon.
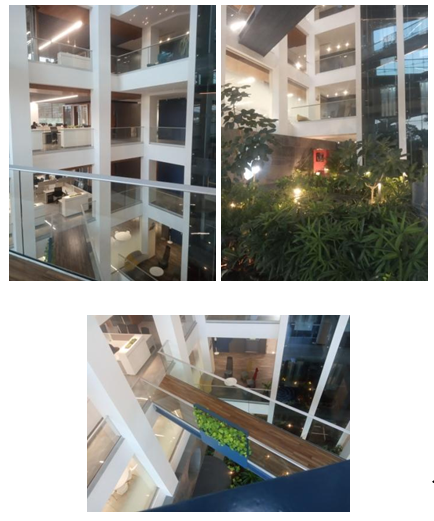
What keeps maintain quality of air is the interesting exhaust system. The office follows an open seating plan. All the floors open into an atrium, which has some lovely foliage at the first floor level. At the top of the atrium you have a glass roof. And next to it are ducted openings where the heated air is exhausted out. Cleaning the glass roof, especially from the insides, is a challenge. It is done once a year by acrobats who hang out from rails built into the beams that support the roof. There is some greenery present near almost every workstation. Basically, low maintenance plants with waxy leaves. They are planted on a substrate which needs to be watered only once a week.
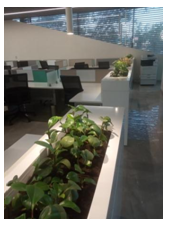
Some energy is consumed to help them with photosynthesis. LED lights have been placed above each plant. And the lights come on whenever the workspace lights are switched on. Fortunately, that happens only in the evenings after the sun has dipped in the horizon. Till then the building allows enough natural light to come in, and there is no requirement for workspace lighting to come on. This is achieved by the use of glass walls on the southern and northern sides. Though one thinks that glass is going to convert the building into a heat island, it does help in getting natural light in. Am not sure if in the total energy math, we will be better off spending an incremental lighting load to reduce cooling load. The East and West facades of the building are not glass. These are the directions which generate the highest heat loads. The Southern side has also got louvers on the outside till 50% of the wall height. This is to keep direct sun out of the work areas. On the northern side, which sees more of the sun coming in, work area start 1.5 m away from the wall to achieve the same effect.
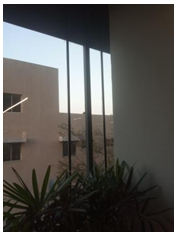
Offset from North Wall
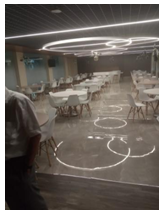
There is a lovely eating area on the second floor. Food is bought in by a contractor. Am told that Friday lunches are special. Sat and Sun are weekly offs for the Enpro office. The factory works on Saturday though. My next agenda would be to land up around lunch time on a Friday to be able to partake of on the feast. The eating area does not open out into the atrium, it is blocked off by a translucent glass wall. Instead separate exhaust fans have been installed which take out the lunch time air.
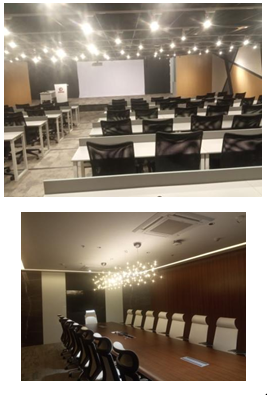
There are a lot of meeting rooms in the building. 5 are named after continents. The largest one is an auditorium called the Universe. The audi requires conventional air conditioning. It gets used a few times a week for training programs and town hall meets. What I liked best was the sports area on the ground floor. There are two table tennis tables and a badminton court. The next visit agenda would be to spend some time at the TT table too.
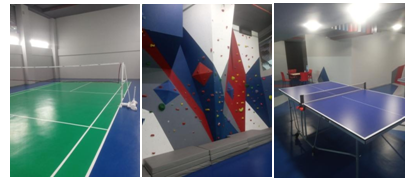
What sets aside Sri from a lot of other green entrepreneurs is his personal commitment to the environment. Both Sri and Anuj cycle down from their house in Pradhikaran to the Pimpri office every day. The eco friendly Karkares celebrated Anuj’s marriage in quite a hatke way. The baraat cycled from Nigdi, where the Karkares stay, to Lonavla, where the marriage festivities were being held. Anuj’s wife is an MBA from IIM Indore and works with PwC. Following the example of the leadership, there are 50 more people of the Pimpri team that also cycle to work. As a small token of gratitude, these folks are given free meal coupons, a kind of fuel allowance for their cycles if you please. For folks who get EVs to work, there is free charging available.
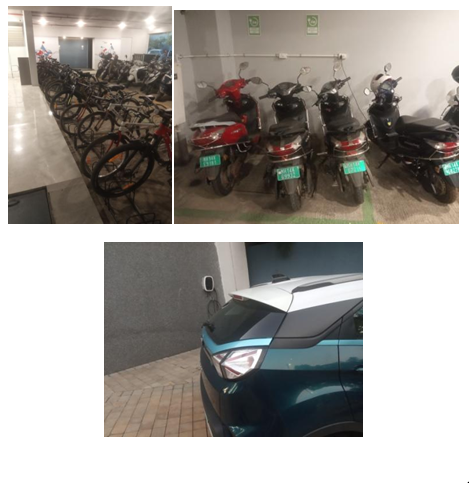