Vijay joined Xytel after his 7 year stint at Vigyan Ashram. Xytel had a JV with Powergas for making pilot plants. The company got taken over by a competitor in 2005, which is when Vijay decided to leave – and set up Texol with a few of his old colleagues. He had a house in Bhosale Nagar, which he sold off – and moved to Bavdhan. He rented an open plot of land on which a prefab shed was put up- and they started making their projects there. The company started running short of space. And in 2013 they shifted to the current site near Sutarwadi.
A small patch of kaccha road leads you to the factory. The hillside plot ensures a great view – and Vijay’s better half has done a great job of landscaping the factory. Fun fact: his better half moved from microbiology to botany over the years. During the couple’s Pabal days, she used to run a pathology lab in Rajgurunagar. After Vijay left to join Xytel in Mumbai, she shifted to Pune and worked for a few years with a lab in Pune. But her interest was more in gardens – and she turned that interest into a business. She has set up more than 300 gardens – ranging from terraces to 1 acre spaces. After Covid, she works mostly at the factory – and also at the small farm that the couple owns close by.
Vijay’s daughter studied at Aksharnandan. Vijay was once called to take a workshop on basics of electricity for the kids at Aksharnandan. He took along a battery, two switches, two bulbs and some wires. He handed them over to kids – and their first assignment was to make the bulb glow. Next assignment was to also be able to switch the bulb on and off. After that kids were challenged to light two bulbs – with each of them being independently switched. In the entire process, Vijay gave no instructions. It took an hour for the kids to figure out how things work. After that Vijay took them through the theory of series, parallel and logic using switches. Kids understood everything. Doing helps learning.
We had a lovely lunch at the canteen which is located in the basement. On a hillside, there is actually no basement because the view was as good as it is from Vijay’s third floor office. We then went to the shop floor for a factory tour. There is a pit, whose floor is at the canteen level. This pit is used when the Texol team needs to construct plants which are super tall. The roof is 10 m high – and with the 4 m pit, they can make structures which are up to 14 m tall. Vijay informs me that they have used the pit more than 4-5 times in the last 10 years.
Texol has developed working knowledge in a wide diversity of fields in the chemical industry. Though they are not masters of any specific process, their general knowledge is of great help when coming up with new designs. I could see a pilot plant being put in for trials for an insecticide manufacturing company. The components that go into a plant are: reactors, pumps, panels, sensors and gauges, pipes and the structure. The structures are designed with ease of transportation in mind. No structural component exceeds the dimensions of a 40 ft container. The reactors are mostly made in SS – and these vessels, like the structures, are also made in house. Apart from the welding and assembly areas, I could also see a few machining centres.
Metering pumps are also made in house. And that requires a small diversion. https://vkpumps.com/ facility is right next to Texol. The main unit is in MIDC Ambad at Nasik. VK is India’s leader in the metering pump space. MB Bhave, who started VK Pumps, was a bachelor. VK is a much older company than Texol, and incidentally my friend Srikrishna Karkare of Enpro started his career as a sales engineer at VK pumps. Texol was a customer of VK – and was approached by MB Bhave to take over the company. There was some synergy in the product line – and Vijay ji decided to go ahead with the deal. Within a year of the sale, the old owner passed away.
VK’s metering pumps are mostly the reciprocating type. They have an adjustable linkage which alters the length of the stroke. By using different combinations of stroke and motor speed, you can dispense flows as low as 0.04 liters per hour to a few cubic meters an hour.
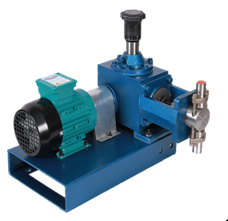
VK’s metering pump
During the lockdown there was a downturn in business. Texol was approached by Alfa Laval to supply vacuum pumps for their milking booths. These vacuum pumps are connected to the milking cans – and they create a suction through the milk column that exists in the flexible pipe from the can to the cow’s udders. This is achieved by pumping air out of the column that exists over the milk surface in the can. This is done in pulses. All of this results in a very gentle pressure on the udder and eases milk flow. Traditionally these pumps had been imported from China, but there were recurring supply issues. So Texol was called in. Texol already had expertise in vacuum pumps because a lot of pilot chemical plants do require vacuum. They came up with a simple design which uses a rotating impeller and creates a vacuum of 0.5 bar.
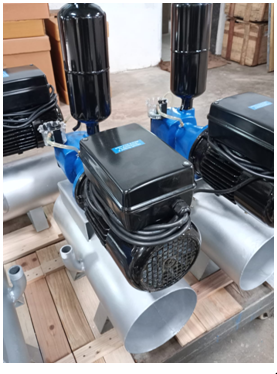
Another interesting Texol client is https://lanzatech.com/, a company that works in converting CO2 to ethanol. This multinational is currently working with an oil refinery in Panipat. The chemical composition of the chimney gases at the refinery vary with differing inputs. These gases are used as feed to a bacteria solution in fermenters which do the job of converting the CO2 to ethanol. I wonder whether they add some other nutrients in the feedstock? The gas needs to be treated to maintain safe levels of non CO2 gases for the bacterial culture. This requires the company to continuously analyse the exhaust gases and tweak the cleaning catalysts. Texol has created a lab in a container for this analysis. It is a mini pilot plant with storage areas for all kinds of gases. There is an analyser and a refrigerator to store chemicals. We took a round of this container – and was impressed by the quality of the workmanship.
The high point of the visit was meeting the technician who single handedly put the Lanzatech container together. Our friend used to be an auto rickshaw driver before he joined Texol. He has been educated only up to grade 3. Vijay has been using the Vigyan Ashram strategy of hiring 10th fails at Texol too. And it has worked wonders. Texol technicians routinely open imported equipment that has failed without any idea of what to expect inside. And most times they are able to use their practical wisdom in repairing the equipment. These technicians now travel all over the world installing plants.
Vijay ji narrated an interesting story about the same grade 3 passed technician. He was once deputed to Saudi Arabia for a plant commissioning, along with an engineer. Because of a family emergency, the engineer had to fly back home early. The technician was asked to stay back for two days and complete the job. After a successful installation, our friend reaches the airport to realise that the travel agent has given him a ticket in the name of the engineer. The wrong cancellation had been done. The Saudi visa policy is such that any overstay can result in a jail sentence. Thinking on his feet, our friend realised that the initials in the name of the engineer, SB, matched his own. He convinced the immigration official that his actual name is much longer – and the SB represented his own name, albeit printed incompletely on the ticket. Our friend was allowed to board the plane.
Real education, as per Vijay, is not time spent staring at screens, but time spent working with your own hands. Graduate engineers who join Texol end up being mentored by these technicians in understanding how things come together in a pilot plant. Texol technicians are just handed over basic drawings – and end up putting together all the wiring and gas pipelines based on these. Putting up a gas joint requires perfect finishing of pipe ends and an exact 1.25 turns of a ferrule. When the plant is put through a end of assembly quality test, the pressure vessels are kept filled overnight – and pressure drops are then checked. Even with the hundreds of connections in a typical pilot plant, there are very few joints which require rework. Self certification by a Texol technician is good enough.
The Texol eye-for-detail culture is probably a result of Vijay’s own education in design at IIT Bombay. I asked Vijay why he chose to not get into more conventional ‘product design’ after finishing his M.Des course. Vijay jokingly refers to the two years at IDC as those of ‘dabba design’. Unlike most engineers who join design school, Vijay did not come to IDC to run away from engineering. One of Vijay’s professors was reviewing his Vigyan Ashram geodesic dome design at a conference which Vijay was also attending. He asked Vijay to think of ways in which the bolts of the dome could be hidden. Vijay’s point was why do we consider bolts to be uglier than the structure. He feels that design school should focus more on solving problems that benefit society in a larger way. More function, less form.
To illustrate how both of his fields of his education work well together, he recounted an interesting design problem that he helped solve for Phillps many years ago. Those were the days that Phillios made incandescent bulbs. The tungsten filament was made of very fine wire. This wire was wound over a molybdenum core. And to take the core out you dissolved it in a mixture of nitric and sulphuric acid. This would happen in acid baths in one corner of the Mohali plant. And it was all done by manual labour. No one would last more than 3 months in this job, given the fumes associated with handling the acids. A visiting diretor from Holland was stunned when he saw this arrangement – and told his local team to automate this process asap.
The Phillips team sought help from NCL – who in turn asked them to meet with Vijay. Vijay and team came up with a very elegant solution, where the molybdenum-tungsten filaments were placed in a glass jar – and needed to be taken out a few minutes later, with the molybdenum removed and with two water washes done. All this without any human intervention. Not only were the fumes washed out before being exhausted, an added bonus was a small plant which recovered the molybdenum from the molybdenum sulphide that formed in this process. The Dutch directors were so happy with this design that they ordered two more units of this equipment for their Holland plants.