Bhushan, Pinki and yours truly started at 0645 hours from Sancheti hospital. Anil had misplaced the keys of one of the new standby battery packs that we had borrowed from the Felidae team. Thanks to this loss, he discovered that he can fit the pack even without a key. We caught up with Giri at the Kharadi Bypass. Cycled to Koregaon Bhima and had a breakfast stop at Shivneri misal. The special misal we ordered was swimming in non vegan stuff: Dahi, Taak and gulab jamun. Defending my new found spirit of veganism, I passed all the milk infused stuff to the non-vegans in the group. There were also complimentary mineral water bottles with each misal, Ugh! We bartered those for some extra ussal.
Pinki had planned to ride with us up to Ranjangaon, but we dissuaded her. She returned back with Giri and Bhushan. (She had only touched level 4 by the time she reached home, Ravi ji uses level one continuously, so his battery consumption is higher. I still need to take up the battery issue with Jai in Chennai.) From Koregaon onwards, Anil and Yours Truly went into comfort mode of using battery, now that the group had shrunk down to just two. I used mostly Mode 1 of pedal assist, at times mode 2. Anil used mostly mode 2 – and had to use the spare battery he was carrying. One of the reasons for mode 2 was that he prefers his tyres to be under inflated, as he has faced issues with punctures with his current tyres. I think it’s time for him to change tubes. Having fully inflated tyres is a must in any long distance cycling, especially where the power sources are limited. With no major ghats we averaged 20 kmph. And were not fatigued. The pedal assistance would be switched on at the smallest gradient so that the human energy output would be a steady 50 W.
Would I carry a spare battery next time? 100 to 125 km is a Goldilocks distance for long distance cycling vacations. You need to plan to reach around lunch time, so that post lunch sessions can be spent with friends, visiting places. Ideally both together, so that the cycles can be given a rest for the rest of the day. I think a lunch time top up should carry me through for a 125 km ride without a spare battery. But if you are more in level 2, then the spare battery is a must. Thanks to the electric assist, we made it to Nagar in time for lunch. My friend, Aditya Fatangere, had recommended Hotel Sachin, located on the highway about 3 km before Ahmednagar municipal limits start. We invited my friend Sudarshan, also an E2O Owner, to join us for lunch there. Sudarshan is a CA who heads the finance function at the Schneider Switchgear plant at Ahmednagar.
We came to know later on, that Hotel Sachin is an employee run hotel. In case you started imagining owners who have inclinations to socialism, pause. The reason it is employee-run is because the entire owner’s family is ensconced in Ahmednagar jail! There is an equally popular hotel across the road called Sandeep. Not sure of the location of Sandeep’s owners. We had the signature gravy of the hotel – a very spicy kala rassa veg kadai with bajra and jowar bhakris. Was a bit too spicy for my taste. I had to ditch my veganism and put some desi ghee into the gravy to ensure that the tongue does not get charred. Post lunch, we parked our cycles near the railway station, where one of our fellow E2O owners, Dinesh Munot, has his house.
Went on to have a dekko at the tank museum run by the Indian Army. I wonder about the utility of tanks in today’s warfare. A lot of the bomb dropping work can now be done by drones. Modern warfare is about having smaller, more numerous distributed assets rather than a few big ones. Maybe tanks and fighter aircraft will become as rare in the army and airforce as aircraft carriers are in the navy. It was interesting to see the variations that have been made in terms of tank design. The track mechanism ensures mobility over all kinds of terrains. has been so that it can traverse all kinds of surfaces. was interesting to note the presence of a Tyre and track tank. You can possibly steer it better. Here is a tank quiz – disclosure – it only consists of questions whose answers I don’t know.
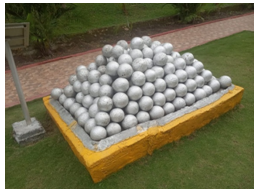
How many cannon balls are there in the above box?
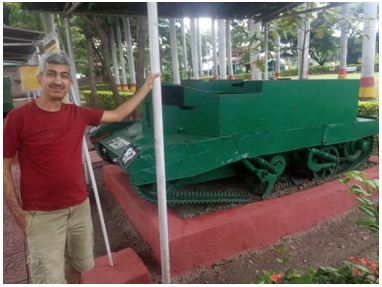
How many people can you seat in the baby tank featured next to Anil?
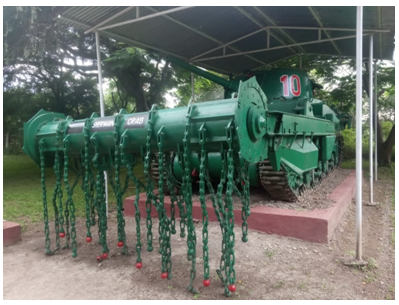
What agricultural (or non agricultural) application was this tank put to use for?
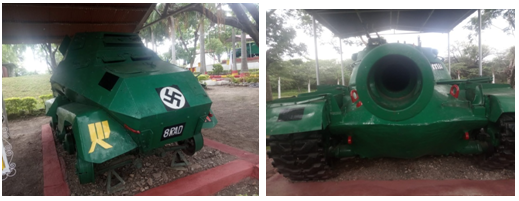
What would be the ratio of kerb weights of the two tanks featured above?
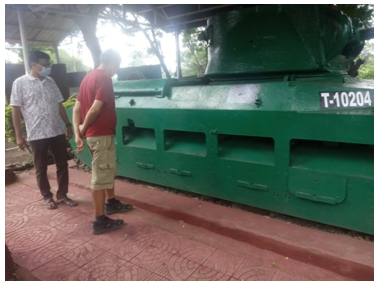
Why do the tracks of this tank also get armour cover?
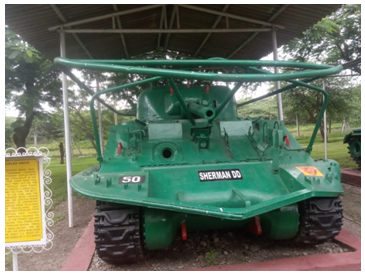
Why were the tubes welded on the top of this tank?
If you can read the font on the yellow poster next to the tank, you may have the answer to this question.
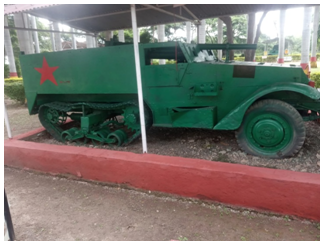
Why did the designer decide to make this tank a front wheel drive?
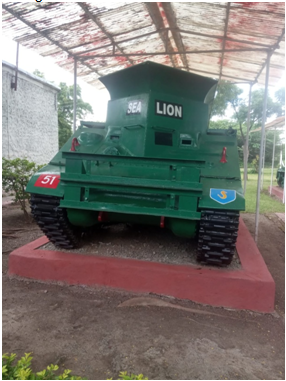
How does this Sea Lion propel itself in water?
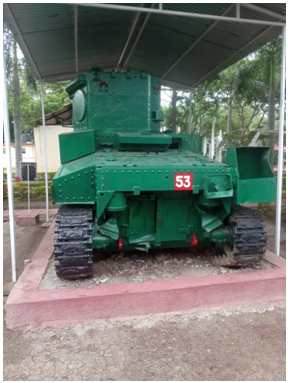
How many years old is the tank above?
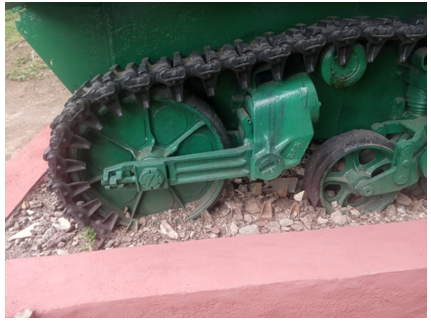
What purpose does this mechanism serve?
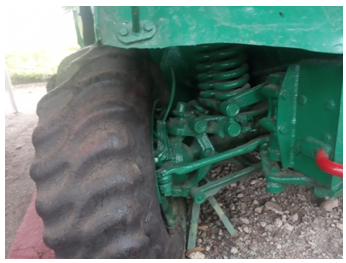
For automobile engineers, what kind of suspension is this?
After the museum visit, we came back to have chai with Dinesh ji. He has a manufacturing setup in Nagar where he does machining work for ZF steering amongst others. The Munot family has a fleet of 10 cars, which includes an E2O which has run 200,000 km. Looks like the granddaddy of the E2O family. Dinesh claimed that he has spent almost Rs. 200,000 in repair bills. I would still think of it as value for money. Dinesh has installed a range extension kit from Hemank. Sudarshan was inspired by this – and got his car also fitted with the same pack. Both are satisfied customers with the packs doing good. Dinesh and Sudarshan have both got white E2Os. Sudarshan has put a Manchester United sticker on his own vehicle, so that his friends realise that it is Dinesh and not Sudarshan who is regular at bar hopping. Dinesh showed us his DC modified Innova with recliner seats like the new Toyota Velfire. Dinesh likes driving himself around. He feels that India is not yet ready for electric cars. Dinesh narrated his typical use case: Nasik, Mumbai and back to Ahmednagar – all in the same 24 hours. It’s not possible to have done this with an electric vehicle. The moot question: is the car the master or a slave. I tried convincing him about fast chargers, but he was not too happy about it. The Munots are thinking of buying a Tesla when it launches in India, in large part because of range.
Sudarshan knows the Munots because they are vendors to Schneider. We discussed Sudarshan’s work at Schneider, where he heads the finance function at the plant. He spends his time equally between MIS, Costing, accounts and a little bit of production liaison. Costing is what he finds most interesting. Sudarshan is very happy with life at Ahmednagar. Feels that he knows half the town by now. And indeed he did because when I told him that I am meeting with Aditya Fatangare, he also got invited for the dinner, as he knew the Fatangeres.
In between we also found time to visit Avatar Meher samadhi. It is on the way to Daund from Ahmednagar. There is a pedestrian underpass below the railway line to get to the samadhi. The landmark is the township of Meherabad on the Daund road. The culture at Meherabad is a bit like the Osho ashram in Pune, with a fair number of foreigners. Or maybe a mini Auroville. Meherabad township has a guest house, but it was not open for outsiders, thanks to Covid. Should plan to come and spend one week there. Most of the residents have not met Meher Baba, even the old ones. Expected, since Meher left the planet the same year I was born, in 1969. There is some spirit of Meher Baba that they see inside the premises. I read the Wikipedia article on Meher – and I find that he was the originator of a simple philosophy, later on made famous by Bobby McFerrin’s song – ‘Don’t worry, Be happy.’ He believed that the world we live in is all maya – imagination. And what is the only real thing is a God that exists inside each of us. Most of his bhakts flock to Meherabad, I guess, in order to discover this god inside themselves.
One interesting thing was that Meher did not speak anything for 50 years. The samadhi seemed to be still immersed in that silence. We walked around his house. Very well kept old structure, with a tower rising above. There are a lot of open grounds around. Met with Ted, from suburban New Jersey, who has been staying here for 44 years. I asked Ted how he manages his own cash flows. Ted inherited a little bit from his parents – and did not need to work. The trust has given him a place to stay but he has to manage other things on his own. He does some volunteering work at the ashram, and he had just got a painting job done near the samadhi. Like Auroville, most of the residents are in their sixties and seventies. The question is how do you ensure that the baton passes on to the younger generation. Will try to find answers to this question on my next visit.
We then had a quick shower and change of clothes at Sudarshan’s house and moved on to Aditya’s place for dinner. Was impressed with Aditya’s frugality. They have a lot of property in the city but they continue to live in a small house in a congested area of Ahmednagar. His dad had just come back from a visit to a 20 acre farm that they own near Ralegan Siddhi. Farming is more of a hobby for him, there are hardly any financial returns from agriculture. They have a Bharat Gas agency from 1983 – and a godown in one of the prime areas of Nagar – Pipeline Road. We passed that the next morning. They are planning to shift the godown to an industrial area.
Aditya has got about 35,000 customers for his domestic LPG business. They have tried delegation, but that has not helped. A lot of the challenges in the retail business are related to pilferage and black marketing. They can get into trouble with Bharat Gas because of this. I think he is working on getting the domestic LPG business to run on auto mode. It will be interesting to see the systems he designs to plug leakages in his retail business. Aditya has put in a lot of energy into developing the commercial business for Bharat Gas. He has customers not only in Ahmednagar but also in Aurangabad. Aditya tried his best to convince Anil to switch over his tinning line from electric to LPG. Anil had a demand of 2 commercial cylinders a day. Following up to get the cylinders was a big problem. So he switched to electric heaters. Aditya suggested that he go in for a 440 litre jumbo LPG cylinder, but Anil was still not convinced.
Aditya has an interest in automobiles and wanted to know whether he can do something in the EV space. I advised him against getting into EVs. Instead get into some fee based income from his existing customer base. Maybe an energy conservation consultancy. I can put him in touch with a few energy audit people and he can try to help customers reduce their energy bills. It runs contrary to his own profit motives, but it will help generate customer loyalty. The other idea is to get into some agri related businesses. That seems to be an interesting thing to do. My suggestion would be that he can have a tie up with the Ahmednagar municipality and take over their wet garbage processing facility. Can introduce him to Priyadarshan and his biogas facility. The methane that comes out can be compressed and supplied to existing Bharat Gas customers.
Good news from Aditya is that he is now engaged to be married to an IIM K passout, who used to be his colleague at Reliance. She is based out of Bangalore and is currently working with Amazon. Her family hails from Mangalore. The Fatangeres are now constructing their own new house, partly for impression management for the new bahu and to entice her to shift to Nagar. The date of the marriage is not fixed yet. The future in-laws are expected to come for an Ahmednagar visit in a few months time. We finished dinner and returned with Sudarshan to his place. Sudarshan had offered that we could stay the night at his place. We accepted his offer promptly. He has a lovely two storey bungalow, not very far from Aditya’s house. His wife and daughters were visiting Pune, so we had the house to ourselves.
Day 2
We started in the morning at 6:30 hours. Sudarshan accompanied us to the main Nagar Aurangabad highway. Raj D was waiting there for us. Raj works in telecom related software. Chatted with him for 15 minutes. His wife had packed some atta biscuits for us. We had had a very heavy dinner at Aditya’s place, so we decided that breakfast was going to be only fruits and the atta biscuits. Started our highway journey at 0700 hours. We had to cover 70 km to reach our first destination of the day, Kaygaon Paper mills. There was an interesting ghat going down, about 20 kilometres from Ahmednagar. We reached Newasa fata and changed our mind about breakfast. Had poha and black tea. Reached Kaygaon Paper Mill at 10 45 hours.
Akshay Rathi, my friend who is the managing director of the company, was busy with work at the Aurangabad office. He had asked Nitin Patil, the general manager, to show us around. Nitin was a great host. We started with a discussion on conventional paper manufacturing which uses bamboo. The first process is called chipping – which is breaking down the bamboo to small chips. Then these chips are put into a digester where it is mixed with caustic soda. This causes the fibres to swell – and detach themselves from the lignin, which is the natural binder in any wood. The separated lignin is typically used as boiler feed. I asked Nitin if we can use it again as a binder for paper – but there are issues of smell and cost.
Kaygaon in contrast works totally in recycled paper. The energy usage with recycling is about 240 kWh per ton for a recycled paper plant, in contrast to 1100 kWh for virgin paper. Even water consumption shoots up from 1500 liter per ton to 10,000 liter per ton. Am not sure if the energy usage also accounts for the coal required to run the boiler. But one project that they are planning is to start a 2.5 MW co-gen plant to recover heat from the boiler exhaust gases. They currently leave the chimney at 170 deg C. With co-gen it will come down to 130 deg C. The raw materials for the plant are bales of corrugated box scrap. Daily consumption is about 230 t, which yields about 200 t of paper a day. Most of the difference is because of the excess moisture in the scrap, and also the plastic waste that comes in along with the scrap cardboard. Scrap is mostly imported from European and middle eastern countries. Most of these carton manufacturers are approved by the Forest Council of Canada. As a result Kaygaon paper also has become FSC approved.
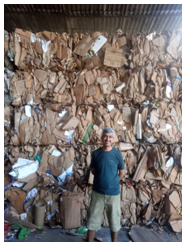
The bales have some amount of plastic and thermocol along with the old boxes. There are almost 3000 tons of scrap at any point of time in the uncovered scrapyard. The raw material has about 10 to 12% moisture content. I asked Nitin what happens when it rains. The moisture content only goes up by one or two percent because only the top layers of the top bales are affected. The bales are stacked seven high. They have a JCB and a tractor to move the bales around. There is a conveyor onto which the broken apart bales are put in.
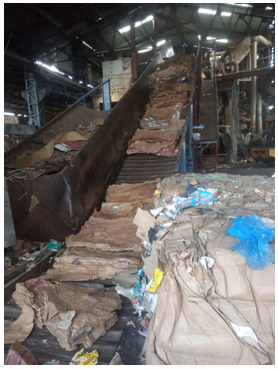
These bales are then dumped into a huge mixer. This is a huge machine with a 500 horsepower motor and 100 HP slurry pump. Waste water from the plant is used to make a slurry of the scrap boxes. Incidentally, there is zero water discharge from the plant. Most of the water discharge is in the steam and moisture that is generated in the paper manufacturing.
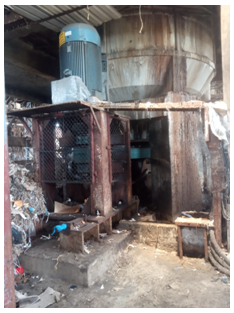
About 2 to 5% of the raw material input is plastic. This plastic tends to float on the top. After every 2 hours, the mixer is stopped and the plastic that is floating on top is taken out. The plant processes about 230 tons of scrap everyday. That means about 500 kg of plastic coming out everyday. This plastic is sent over to close by cement plants for incineration. An incineration facility can be set up at the paper mill itself, and the heat can be used in the boiler. But this requires coordination with the Maharashtra pollution control board and that is something that Akshay is not very happy about.
The slurry goes to a set of three sieves to remove inorganic matter and small pieces of plastic that have still managed to stay in. These three filtration processes involve centrifuges, sloping and rotating sieves. The material is then pumped to the main paper making machine. Turbulence is generated through air pressure. The feeder is given a lateral movement. The slurry at this stage has a solids content of about 1% only. This is poured on to a conveyor belt to form a 2 mm thick sheet on the polyurethane sieved belt. The speed of the belt is about 200 m per min. This 2 mm sheet is doubled in thickness by adding one more sheet later on above it.
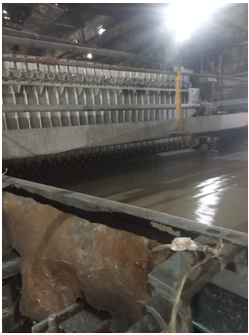
About 2% solid mass density is obtained because of water that flows out during the initial 1 metre or 2 metres. The small lateral movements are to ensure mesh formation of the fibres. The fibres are between 4 to 6 mm long, and have been broken down into single fibres. Diameter is between 0.1 to 0.15 mm. There are some flocculation chemicals that are added as the fibers have a negative charge on the surface and so tend to repel each other. The flocculation chemical is cationic.
There is a very interesting process for getting solids up from 2% to 3.5 %. The belt passes over small blades which are kept at an angle of 0.5 to 1 degree. As the belt passes over these wedges, a natural vacuum forms below the belt on the trailing edge. This vacuum helps in water removal. After this stage, you have multiple stage vacuum chambers which are connected to a central vacuum pump.These chambers help evacuate some more water.
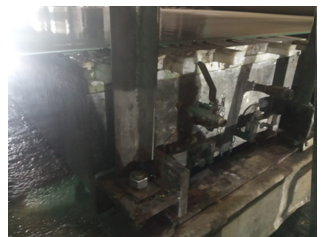
Once this is done, the paper has achieved enough rigidity to leave the conveyor and start moving on its own. Before it leaves the supporting belt, water jets trim the edges so that standard widths can be obtained from the machine. Time for mechanical pressing to start between rollers. One of the final stages of pressing uses a giant 1.5 metre diameter roller, which is basically made of cast iron with an SS sheet on top. The SS sheet has been buffed to achieve a smooth surface. This ends up giving a glaze to the paper. The steam heated rollers use parabolic thermal settings, starting at 55 degree Celsius going up to 95 and then getting down to 55 again. Towards the end, depending on requirement, there is a layer of starch that is put on to the surface. This starch is typically made from maize. It helps give some water resistance to this paper and also helps improve the burst strength of the paper.
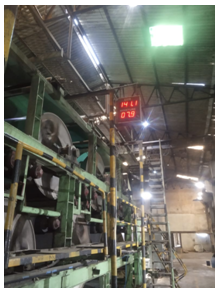
There is continuous scanning going on at the end with a hi-fi Krypton gas filled machine to monitor moisture and gsm. The mill can produce paper from a range of 95 to 250 gsm. This paper thickness profile is shared with corrugators so that they can be assured of the quality. Another interesting test is the ring crush test, which determines the stackability of the cartons that are made from Kaygaon’s craft paper. At the end of the machine, the moisture content of the paper is between 5 to 7 %. There is about 200 kg of finished goods waste that is generated every day during the changeover between paper rolls. I wonder if it can be converted to sheets and sold separately. About 50% of the paper produced is exported.
Nitin treated us to an excellent lunch and black tea before we departed for Waluj. We asked Nitin over lunch, what were the challenges that he was facing. Margin management. Raw material is priced at Rs. 23 per kg and finished goods sell at Rs. 33 per kg. With a 12% wastage, the effective cost works out to Rs. 26 per kg. Energy cost is 290 kWh @ Rs. 8 per unit – Rs. 2500 per ton. The 20 tph boiler uses 350 kg of coal to supply the steam required for producing 1 t of paper. Coal cost per ton of paper is 350 kg @ 6 per kg = Rs. 2100 per ton. That leaves a contribution of Rs. 2.4 per kg to cover labour cost, other factory overheads. The margin ends up at around 5%.
Nitin believes that acquiring and retaining the right talent is critical to margin management. He wants to start with operator level training. I suggested that we can have a thinking related training program that Padmanabh Kelkar has been conducting in the Kolhapur region. Have offered to come down and do a trial program. Can also become involved in this training. on a pro bono basis. One of the problems that the company is facing is water logging. The plant is very close to the Godavari river and the water table is high. You can find water at just 3-4 feet depth.
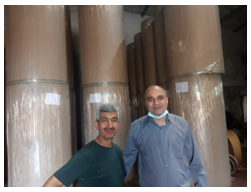
I suggested a subterranean network of pipes around the boundary, which drains the water into the lower end of the factory. There is a consultant that I know in Pune, Constrotech, who has done good work for me in our basement water logging problem. I have passed on the contact details to Akshay. Another suggestion was to have the right slopes on floor areas where the water handling is high. Whenever there is a failure in a pump, the excess flow of water tends to form puddles. It would be a good idea to have drains and trenches along the building walls. This water, along with the flood water in monsoons, can be recycled for process use.
We started around 1545 hours from Kaygaon. Had to stop for half an hour en route close to the Bajaj Auto plant, because of a sudden shower. A lot of our clothes got wet, not only what we were wearing, but also what we were carrying in our bags. Reached Rajesh Kothari’s factory at around 1745 hours. He has been in business since 1995. The first three years were at a MIDC Bhosari factory where he worked with his mom’s brother, who was then making driveshafts for Maruti Udyog. Got inspired to become an entrepreneur. His father was earlier working with Bajaj tempo. Then he tried some farming. which did not work out. Then his dad got a job at Kinetic, Ahmednagar. He stayed on over there till retirement. Rajesh shifted to Nagar when he was in grade eight. He considers Nagar to be his true home, because that is where all his friends and social networks are. He plans to settle down over there in a few years. They have their own bungalow which is still used at least once a week.
His grade 8 friend from Nagar school days went on to become his business partner. Both started two factories, one in Nagar and one in Aurangabad. Aurangabad was where most of the customers were so most of the expansion was in Aurangabad. In 2015, Rajesh mooted the idea of shifting to Aurangabad and becoming a more active partner in the Aurangabad business. It was a 50 50 partnership. But the partner was not very happy with this idea. He advised Rajesh that it was time to split. The business was valued at about 7 crores. Rajesh got a share of 3.5 crores as his part of the business. The initial plan was that Rajesh will get 50% of the business’ customers, but that did not happen. Rajesh used the proceeds from the sale of the business, took some loans and went on to invest Rs. 5 crore to start a unit in Waluj.
There are six lines of vertical milling centres, CNC lathes and also two very noisy forging machines. Rajesh realised that the forging machines should have been put on to the rear side of the factory, which has a separating wall. But by the time that Idea hit him, an investment of Rs. 10 lakh had already been made in the foundation of the machine. So shifting it will be difficult. There is an induction heater right next to the forging machine. The heater takes a massive 150 KW of power. The blanks are basically cut from rods. The ends are removed because they tend to be very hard. This is because the manufacturer uses a flame torch for cutting the rods.
I asked Rajesh if we can use the heat generated by the induction furnace to preheat the rods that are going into the induction furnace. He liked the idea and has promised to explore the same. It takes about Rs. 2 to 3 for heating a single gear blank. If he can recover Rs. 0.5 out of this energy bill, it will add to the margins. In the automobile industry, margins are typically in the low single digits. So every paisa counts.
Rajesh is looking at diversifying away from engine related parts. He has found a good customer in Ahmednagar based Classic Wheels. They supply about 800000 rims annually to almost every major Indian automobile manufacturer. Thanks to the Make in India policy, a lot of manufacturers are now being nudged to buy alloy wheels from India. Till date most alloy wheels are being imported from China, thanks to very low aluminium prices in China. Classic wheels has put up an alloy wheel plant in Nagar. Rajesh has got an order from them for making the metal inserts where the tyre shaft gets fitted. Classic Wheels today accounts for about 40% of Rajesh’s total 1 cr monthly business.
He has a total labour force of about 80 people. The margin is just 3%. RoI comes out to about 36 lakh/5 crores = 7%. He needs to at least double his turnover to get a reasonable return on his investment. He is in talks with Siemens. The future is going to be in small batch production and not the continuous line for which his factories are designed for. EVs are not going to be a very big business opportunity because there is so much spare capacity that would be available once IC engine production stops. Motors require some amount of machining. Battery packs hardly any.
Our electric cycles were parked at the Waluj factory as it had started to rain by the time we left. We had a lovely dinner at Rajesh’s place. Ended up again violating the non vegan diet. Indira ji, his wife, had made some very interesting almond shira. Had two helpings of it. Spoke to his son Raunak, who is doing an integrated engineering MBA program from Narsee Monjee. The 3 year engineering degree happened at the Shirpur campus, not too far from Aurangabad. He is now supposed to go to Bombay for the two year MBA. Unfortunately, he is still around in Aurangabad, as education is happening offline. Advised him to take up marketing in his MBA. Rajesh asked me whether he should send his son abroad for further education. I feel that that’s not really required.
Another Idea he discussed was whether Raunak should get some experience outside Rajesh’s company. Anil felt that it is better that he join the business immediately. Anil gave an example of his own son, Nirav, who was doing very well in the business, even without any outside experience. I advised Raunak that he should work more in customer-facing roles in the factory. This way he will end up getting more exposure. The hotel where we were to stay at night was in Auric City, MIDC Shendra, about 30 km from Rajesh’s house. We borrowed Raunak’s Access scooter and drove down to the hotel.
Day 3
Kamlesh started from Pune at 0530 hours. He called me to get over the two key press conundrum that a lot of first time users of the Nexon EV face. He got over that and started his journey. Sharyu from the goEgo team joined him in the journey. They took 7 hours to reach Auric City in Aurangabad – with a halt at the Ahmednagar Tata Motors dealer to charge up.
I started the day with some fruit purchase. Did the rounds of Auric City – and realised that it is one of the best industrial parks that I have seen. It is a private industrial park managed by the Shapoorji Pallonji group. The Mumbai Nagpur Samruddhi Expressway is only 3 km away from the industrial area. Could see a large Hyosung factory which makes spandex. Hotel Siya, where we stayed overnight, was located next to Perkins, the Chennai based engine manufacturer. Had an interesting chat with the waiter at the hotel. He used to be an entrepreneur running his own restaurant in his village in Gangapur taluka of Aurangabad. The daily collection would cross Rs. 10,000 on weekends. But he ran into partner trouble and had to shut down the restaurant. I encouraged him to restart business – maybe do it on a smaller scale than earlier. (He had a 3,000 sq ft plot the first time around, for which monthly rent was Rs. 10,000.) He made me some lovely tea – and also told me that he has decided to remain a brahmachari for the rest of his life. I wish I had made that decision 23 years ago 🙂
Akshay Rathi, my paper mill friend, joined us for breakfast at 0830 hours at Hotel Siya. Unfortunately driving his Volvo, not his Nexon EV! We chatted about our observations at the Kaygaon paper mill. He talked about his experiences with an online training program that he is doing with Manish Jain from Delhi. He had to leave early for a meeting at 1100 hrs – and after he left, Anil and yours truly went over to the BG-Li in factory where the goEgo charging stations are going to be made. The goEgo team had still not come in – so we took a chance and tried to gatecrash in any case. The security guy informed us that the senior management was in a meeting with some high profile visitors. We were quite ok with meeting junior management – as there was a lot of time to kill. Fortunately, one of the team members knew that a guest had been booked into hotel Siya by the company – and that got our foot in the door.
It was heartening to know that we were the high profile visitors that the management was going to meet. BG LI-IN is a joint venture between the Rs. 2500 cr Bagla Group and LI-IN Electricals of Taiwan for manufacturing various types of Flasher and Relays. The Bagla group started off with magneto assembly for Bajaj’s Waluj plant in the eighties. They then added refrigerator condensers, fasteners and aluminium pressure die casting. The die casting business has been sold to Mahindra CIE recently. BG Li In is a don in relay manufacturing. They have a capacity of almost 90,000 relays a day. Indian Railways is one of their key customers. Apart from relays they also supply integrated power supplies, point machines and axle counters to the railways. They are thinking of expanding into solid state relays in future, maybe with IoT capabilities.
We finished the shoot around 1700 hrs – and I took the scooter back to Waluj. Anil had already been sent ahead with the Nexon to charge it up at the MG fast charging station 13 km away. It started drizzling almost the time I started. Was a wet dog by the time I covered the 40 km required to reach Rajesh’s factory at Waluj. Anil had reached 15 minutes before me. The cycles had been loaded into the Nexon, but there was space then for only the front seat passenger and driver. My dry clothes were in a bag that was with Kamlesh. Decided that bhigi billi will drive that way to Pune. Anil took over driving duties as I was the AC operator to prevent fogging. Took almost 30 minutes to come out of the Waluj industrial area in peak hours. We drove at 60-80 kmph, but it still took 2.5 hours to reach Ahmednagar.
We reached the same Tata Motors showroom where Kamlesh had charged in the morning. It was 2145 hrs. Our first attempt at getting charging started was aborted because of a payment gateway malfunction. We were charged Rs. 200 for charging that never happened. (The charges were reversed later, according to Kamlesh.) But that meant the PayTM account had run to be recharged. Kamlesh put in Rs. 400 and in the meantime Anil had put in Rs. 500. Richer by Rs. 900, we were successful in getting charging started. We chose Rs. 200 in the menu card, as the charging station computer calculated that Rs. 300 would exceed our battery capacity. In hindsight, we should have gone in for the option which allows you to charge by the unit. That option gives you steps of 5 kWh, which is better than the steps of Rs. 100 on the Rupee option in the Tata Power charger app.
After charging started, we walked into the industrial area to have a lovely dinner of Methi Lasooni and dal at Hotel Suvidha. By the time we returned in 45 minutes, the charge had been completed. Unfortunately we still had only 67% SoC. We had to do about 130 + km, and at this SoC level it was touch and go. Decision was made to add another Rs. 100 worth of juice to the battery. After 30 minutes of trials, the Tata Power charger would still not let us get into charging mode. It continued giving us an error code – ARC001 or something like that. It was already 2300 hrs by then. So the new decision was that Atul Gopal would do frugal driving and attempt to get home with 67% charge.
The trip meter was reset, so that the average wh per km could be checked for the trip. The idea was to stay in the 100-110 wh per km range. Wet roads or bad roads are both bad for energy consumption. 10 km into the trip, I realised that we were consuming an average of 130 wh per km. This way we would have to spend the night at Wagholi. As the clock struck 12, a brainwave flowed in. Why not do some good aerodynamics management? So the Nexon started seeking out trucks and buses which were moving at more than 60 kmph – and would tailgate them, keeping a distance of not less than 20 ft or more than 30 ft. The wh per km started dipping after that. And we ended the journey with an average speed of 62 kmph and average energy consumption of 111 wh per km 🙂